Understanding Weld Fume Hazards
Know your risks and the controls that can help reduce them
There are many variables when designing a Fume Extraction System, we can help you analyze your operation & design a solution that ideally meets your needs.
Welding Industry
Demand for skilled welding is expected to grow over the coming decade. With this expected growth, aging structures and equipment will need maintenance while new building and manufacturing continue. Welding operations have opportunities to expand, but as they do, a focus on employee health and safety will be paramount.
While each welding facility is unique, the following questions will help you select the most appropriate fume extraction system for your operation.
Weld Fume Hazards
What are the health risks of weld fumes?
- Type of welding process
- Base, filler, and welding rod metals used
- Space lay-out and number of workstations
- Welder work practices
- Air movement and ventilation
What are the fume limits for my facility?
There’s no single guideline for weld fume exposure. Instead, OSHA enforces Permissible Exposure Limits (PELs) for specific metals, reflecting limits over specific periods of time. For example, for aluminum, iron, and mild steel, the PEL is 5 milligrams of particulates per cubic meter of air (5 mg/m3) averaged over an 8-hour period. Metals that are more toxic, including chrome, manganese, stainless steel, nickel, and cadmium, have stricter PELs.
Many welding operations strive to stay within Threshold Limit Values (TLVs) spelled out by the American Conference of Governmental Industrial Hygienists (ACGIH). These estimates of the exposure level a worker can tolerate over a career, are based on current scientific research and may be lower than PELs. A reference to PELs and TLVs is the Pocket Guide to Chemical Hazards published by the National Institute for Occupational Safety and Health (NIOSH). Be aware, however, that your operation may have additional state and local requirements.
What controls are available for weld fumes?
Once you understand the applicable exposure limits for your metals and process, you need to consider ways to reduce those exposure hazards. OSHA recommends a “Hierarchy of Controls” ranked from most to least effective:
Elimination and Substitution — Physically remove the hazard. Stop the use of hazardous materials, if possible.
Substitution — Replace the hazard. Switch to an alternative, such as a different filler metal or coated wire consumables that generate less fume.
Engineering Controls — Isolate people from the hazard. Enclose the space and/or install a local exhaust ventilation system (fume extractor or dust/fume collector).
Administrative and work practice controls — Change the way people work. Alter welders’ work habits or positions, limiting time in high-concentration areas, and/or improving training.
Personal protective equipment (PPE) — Protect workers with the right PPE. Use respirators approved by NIOSH – especially when other controls prove insufficient – and inspect them to ensure proper fit and condition.
Hierarchy of Controls
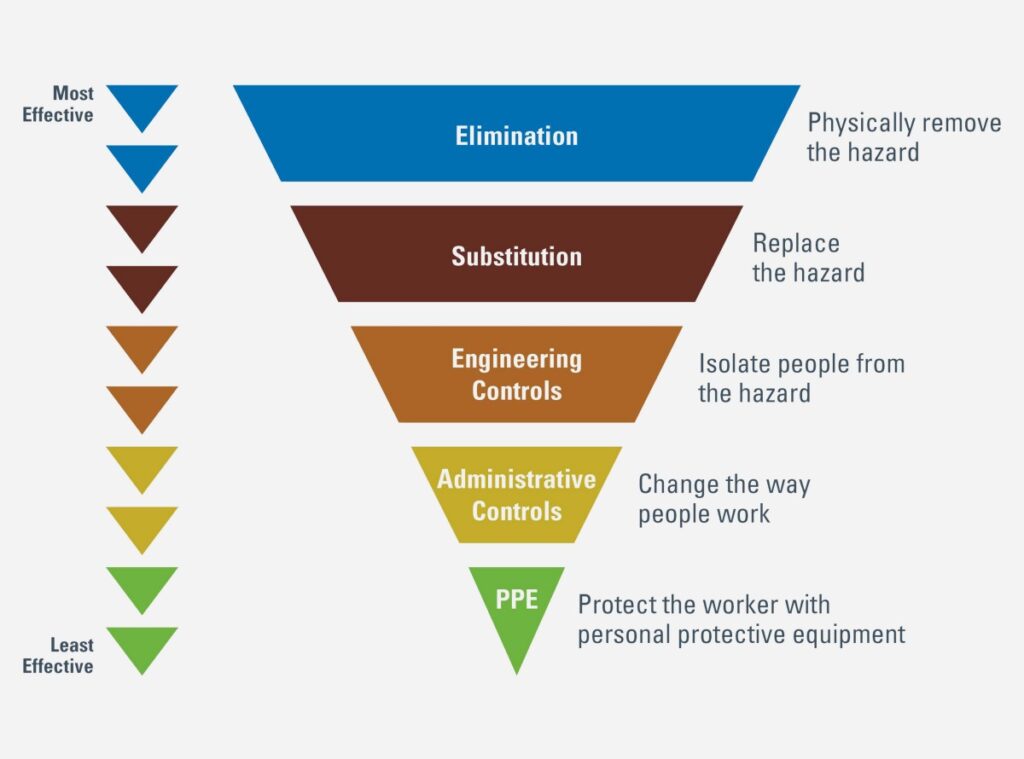
How important is ventilation in controlling fume exposure?
Ventilation is crucial for drawing fumes away from a welder’s breathing zone. OSHA makes these recommendations about natural and engineered ventilation:
- Stay upwind if welding in open spaces or outdoors, although this does not guarantee safety.
- Use local exhaust ventilation (also called fume extraction) for indoor welding.
- Never weld in confined spaces without ventilation.
- Where there is no mechanical ventilation, use natural drafts and position the work to avoid exposure.
While natural or forced-air fan ventilation may work in some circumstances, fume extraction systems are generally much more effective. In fact, in Great Britain, engineered ventilation has become mandatory in welding, even for mild steel. A 2019 update to the Health and Safety Executive (HSE) requires all welding operations to use local exhaust ventilation. Because Europe is often the first to adopt stricter regulations, the rule may indicate a changing landscape for welders in the U.S. and other regions.
Summary
Every welding operation is unique. AST Canada can help you identify applicable exposure limits, sample air from breathing zones around your workers, review your process, and guide you in developing a risk management strategy. In addition, we can assist you in selecting filtration equipment to assist in dust and weld fume collection as a part of dependable engineering solutions.
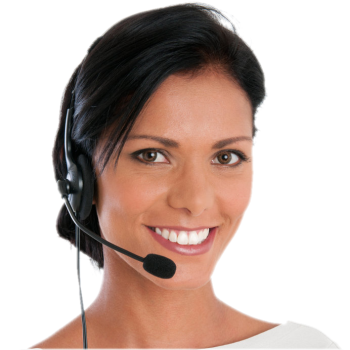
AST Canada has been helping clients find solutions for their unique Dust, Mist & Fume Collection needs for more than 40 years.
We can help you too.
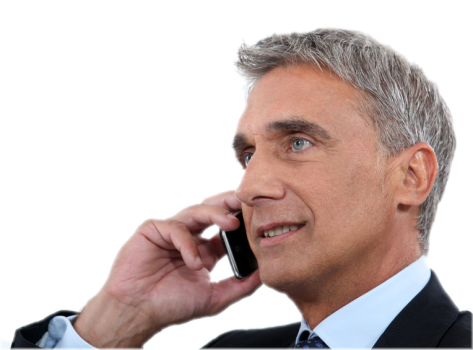