How to Minimize Downtime in Your Mill Dust Collector
Controlling Dust in Milling Operations
Dust control is an integral part of milling. Managing dust is necessary throughout the process: in pneumatic conveying and central vacuum systems; near bag dumps and packaging; near grinding, milling, dryers, and blending steps; and at truck or rail car loading points.
Baghouse dust collectors—the model most commonly used in milling—are rugged machines and rarely break down. But if a disruption should occur, it can be costly because of lost production and repair expenses. It is far more cost-effective to take steps to optimize baghouse performance and monitor equipment than to risk a disruption.
Key differences between planned and unplanned downtime:
Planned Downtime: Minimal Production Disruption | Unplanned Downtime: Increased Production Disruption |
---|---|
Parts can be ordered in advance | Rush shipments increase manufacturing & shipping costs |
Thorough maintenance checks can occur | Hasty/minimized time for maintenance inspection |
Costs are more predictable & less expensive | Costs are unpredictable & higher |
Two Ways to Improve Dust Collector Uptime
Two advancements in filtration from Donaldson make equipment even more reliable and easier to maintain. One is new pleated filter construction, and the other is smart technology that monitors the dust collector’s condition. Both of these improvements can be easily installed on any new or existing dust collector. Here is more about each option:
1. Donaldson Pleated Bags: Longer Life, Better Efficiency, and Easier Replacement
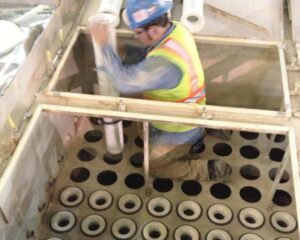
Most baghouse dust collectors use polyester felt bags to capture dust drawn into the system. In many baghouses, compressed air periodically dislodges the dust build-up on the filter to maintain optimal filter performance. The flexibility of these bags is ideal for shedding agglomerative (sticky) material. However, the media can wear quickly with exposure to abrasive dusts. Also, changing them can be time-consuming since each support cage much be removed and fitted with a replacement bag.
With these challenges in mind, Donaldson has developed a hybrid technology: the pleated filter bag. Pleated bags have the flexibility of conventional filters, but are more durable, efficient, and easier to replace—like filters previously available only for cartridge-style dust collectors. (Figure 1)
Here are the advantages of Donaldson pleated filter bags in greater detail:
- Stronger material: Our pleated filters come in spunbond polyester, ePTFE membrane, or fine fiber options. All of these media are more resistant to damage than common polyester felt.
- Capture efficiency: The improved media capture submicron dust particles more effectively and the dust loads on their surfaces, which lowers emissions and extends filter life.
- Compact size: Because pleated bags have double the filtration surface area, they can be half the length of traditional bag filters, which simplifies filter replacement time.
As a direct replacement for traditional felt bags, pleated bag filters can deliver up to three times the filter life of a 16-ounce polyester felt bag, reduce energy use and emissions, and reduce labor and downtime costs by up to 50 percent.
Dust Control
In many plant operations, dust control is an integral part of the production process. Dust collectors handle applications ranging from: filter receivers (commonly used in pneumatic bulk material conveying and central vacuum systems), nuisance dust collection (bag dumps, bin vents, bulk packaging, rail car and truck loading, and belt conveyors), and process ventilation (grinding, milling, size reduction, dryer applications, and mixing and blending).
The most common dust collector in plant operations is the traditional baghouse collector. The traditional baghouse collector uses bag filters, or socks, to remove dust from a conveying airstream. Many baghouse designs extend filter life by using compressed air to pulse clean these filters on a periodic basis in order to dislodge the deposited dust cake and return the filters’ flow characteristics.
Baghouses have been the workhorse in industry for decades. As baghouses age, they need more Tender Loving Care or preventative maintenance (PM) to maintain operation, and the larger the baghouse, the more TLC the bag filters require. Bag filters are typically changed out as the average pressure drop gets too high or with upset conditions that may damage the bags (i.e. bag abrasion, dust blinding, temperature surges, or just mis-application).
Changing filters in collectors can be very labor intensive, time consuming, and – quite frankly – a filthy process. The process of removing filter support cages and then the dirty bags can consume tremendous amount of personnel time. Depending on the quantity of filter bags and the design of the collector, the total time to complete a filter bag change-out can easily exceed 24 hours. Even during planned downtime, this process can significantly exceed the resources plant operations allocated when the shutdown was scheduled.
When upset conditions occur (i.e. broken or abraded bags, premature blinding of the bags, or damaged bags from high temperature excursions) the unplanned downtime escalates into a very time-sensitive, critical, and costly situation. If replacement bags are not in stock, the maintenance manager may have to pay added charges to expedite delivery of replacement bags, sometimes at an added cost of several thousand dollars. Even when the bags are received at the plant, it may still take plant personnel more than 12 – 24 hours to fully replace the bags. Beyond the unexpected cost of the replacement bags and the expedited freight to get those bags quickly, another significant cost to consider is the cost per hour of lost production. In some facilities and industries, such an upset condition could cost a plant well over $250,000 in lost production!
Minimizing Downtime
Part of the challenge in minimizing both planned and unplanned downtime is to reduce the resource hours necessary to conduct a filter change-out while at the same time extending the serviceable life of the filters. In combination, the longer life and the quicker change-out will reduce downtime costs. Given this reality, there has been a shift in recent years from buying conventional bag filters to buying pleated bag filters for baghouse operation.
The Case for Pleated Bag Filters
Pleated bag filters combine the functional benefits of conventional bag filters with the benefits of cartridge filter technology. Pleated bag media is available in spunbond polyester, ePTFE membrane, and nanofiber on spunbond. Each of these media options can optimize the pleated bag filter’s efficiency. Pleated bag media offers higher efficiencies and more filter media in a filter package that is much shorter than a conventional bag filter. As a result of these features, pleated bag filters can offer on average 2 – 3 times the filter life of a traditional bag filter.
How Pleated Bags Minimize Downtime
As a direct replacement for traditional bag filters and cages, pleated bag filters provide longer filter life and less maintenance. Plant staff won’t have to pull a filter support cage and then a filter bag during filter replacement. Installation and removal of the pleated bag filters is quicker and easier due to the one-piece design of the pleated bags. The ease of installation also decreases the dust exposure to maintenance personnel because it is a considerably cleaner process during change-out.
Eliminating the cage and utilizing shorter pleated bag filters simplifies installation and reduces replacement to a fraction of the time. This decreases lost production time and reduces the maintenance and labor cost attributed to changing out conventional bag filters and cages.
The shorter length of pleated bag filters also provides an increased dropout space, which encourages material fallout, allowing heavier, more abrasive-particulate to fall out in the opened space while lighter dusts are filtered by the efficient media. This significantly reduces potential abrasion on the pleated bag filters, resulting in longer life for the pleated bag filters and reduced downtime associated with bag abrasion.
The pleated bag filter can also provide significantly lower pressure drop when compared to traditional bag filters. The increased filter area and higher permeability of pleated filter media presents an easier path for the airflow. A given volume of air per unit of time (CFM) can be processed at a lower pressure drop translating into energy savings. And less energy means lower operating costs, which benefits the plant’s operational budget.
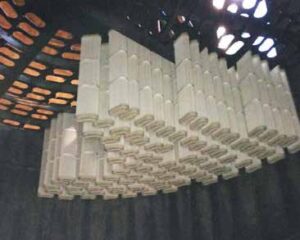
- Reduced abrasion: The shorter length of pleated bag filters encourages heavier, more-abrasive material to fall out of the airstream naturally, reducing wear and extending filter life. (Figure 2)
- One-piece construction: Donaldson pleated filters provide their own support, which speeds up replacement and releases less dust than removing both a support cage and felt bag.
- Lower energy requirement: Depending on collector design, pleated media allows a greater volume of air (in cubic feet per minute or CFM) to move through the collector, creating lower resistance to airflow which saves energy.
2. Donaldson Connected Technology: Real-Time Monitoring and Timely Maintenance
Another way to improve dust collector uptime is to conduct timely maintenance. Hidden problems such as worn valves, or filters too dust-loaded to clean, can cause equipment failures. Yet today, mill owners don’t always have the time/resources to monitor this equipment.
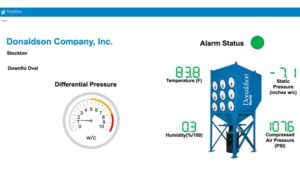
Donaldson has introduced a connected solution for this problem. The technology monitors dust equipment remotely and alerts owners before maintenance actions are required. Sensors placed on the dust collector send real-time data to the cloud, where Donaldson analytics convert it into useful intelligence. The person responsible for maintenance receives insights via a web-based dashboard and text or email alerts. With a laptop or mobile device, a supervisor can keep tabs on many dust collectors across multiple locations. (Figure 3)
The technology can be installed on new or existing equipment made by any manufacturer. In pilots with facilities including mills, the connected solution provided these typical results:
- One facility that struggled with a plugged dust collector hopper twice a month, on average, required two to three hours per incident to fix it. Earlier alerts from the connected technology reduced allowed them to address the problem before particulate built up in the dust collector and the factory, reducing corrective action time to 15 minutes.
- Another facility seeing short filter life could not identify the cause. Data from the connected solution enabled Donaldson’s support team to quickly diagnose that low compressed air pressure led to improper filter cleaning and eventually filter plugging. Once the problem was identified, it was easy to make necessary changes—and get the facility back to normal filter life.
Donaldson’s connected solution can increase production uptime and optimize filter life and equipment function. The results are lower total costs for dust control systems and more time to focus on higher-value production tasks.
Summary
Today, mills have advanced and convenient options for improving dust collector uptime and reducing total spend on maintenance. By installing pleated filter bags and a connected solution to monitor equipment, owners have an effective and affordable combination of strategies to manage dust control.
IoT Enabled with iCue™ Connected Filtration Service
This collector* is now enabled with Donaldson’s iCue™ connected filtration monitoring service. Designed to remotely monitor a facility’s dust collection equipment and provide operational insights directly to end-users, this information can help manufacturers reduce unplanned downtime, support efficient maintenance and operation, and automatically capture compliance data.
* may not be available on all models
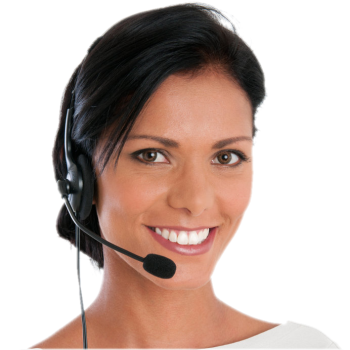
AST Canada has been helping clients find solutions for their unique Dust, Mist & Fume Collection needs for more than 40 years.
We can help you too.
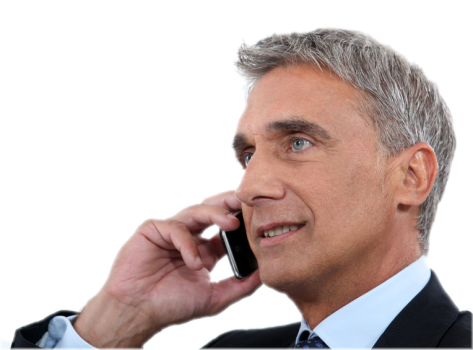