Seven Things to Consider When Purchasing a Dust Collector
Considerations when purchasing an Industrial Dust Collector to help you get exactly what you need.
Do you currently have plans to purchase or upgrade a dust collector for your facility? If so, we advise the following seven considerations to ensure you get exactly what you need:
Industrial Dust Collector Purchasing Considerations
1. What Are Your Dust Control Needs?
Each dust collection situation can be very unique whether you’re collecting wood chips, welding fume, or soybeans; therefore, it’s important to understand not only the dust you generate but also how your processes create that dust. Beyond just determining the required air volume to capture and control the dust created in your process, you should understand and define all the needs in your operation.
As an example, does your process generate dust only under upset conditions, or is dust generated continuously while the process runs? Does your process run intermittently for a few hours a day? Or is it run continuously for 8, 16, or 24-hours a day? If you have multiple processes, do they all run at the same time? Or do some run on different schedules? Each of these conditions influences the number and style of collectors you might consider.
Do you generate enough dust quantity to dispose of dust multiple times a day? Or is dust loading light enough for daily, weekly, or even monthly disposal? Your answer will influence the discharge methods you consider to remove dust from the collector and may suggest alternate collectors with fewer or more hoppers.
Are there regulatory standards you need to meet when returning filtered air into your facility to take advantage of energy savings in heating and cooling make-up air? Or will you exhaust filtered air to atmosphere? If you exhaust filtered air to atmosphere, do regulatory limits exist on the air quality required? These considerations will all have a direct influence on your choice of collector and filter media, and they may drive decisions on including secondary or monitoring filters.
Knowing the details of your operation allows you to make better informed decisions on a dust collector strategy, and helps in the critical step of selecting the proper dust collector.
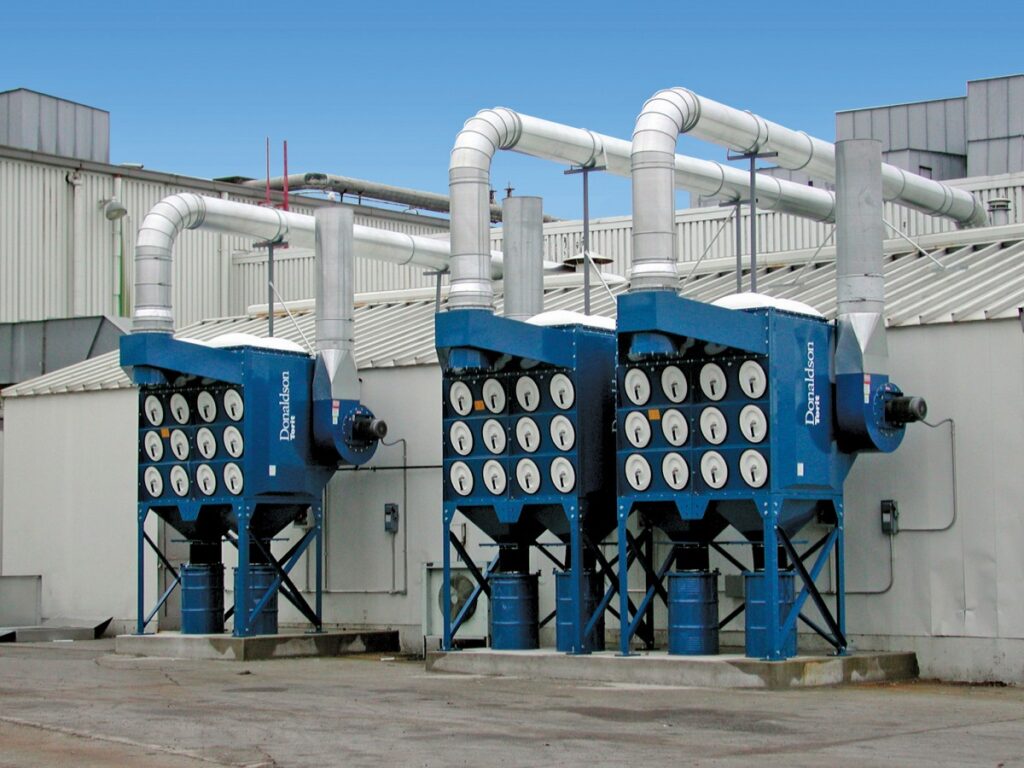
2. Can a Dust Collector Supplier Configure a Dust Collector to Meet Your Needs?
3. What Range of Collector Solutions Is Available for Your Application?
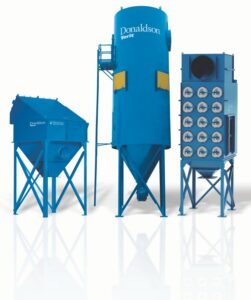
The answers you determine to the first consideration on this list will suggest a variety of solutions – some offering benefits over other solutions. Will your dust collector supplier offer a variety of collector solutions? Or will the supplier attempt to make one collector fit every situation?
Beyond selecting the cartridge, bag or fluted media available on the market, options such as intermittent or continuous cleaning can play a significant role in your collector strategy. Optimizing the match between your process and a collector design can reduce the equipment cost and the operating costs.
You may also save capital and operating expense by using dedicated collectors for parts of your process, rather than centralizing dust collectors for your entire process.
It is also important to consider utility requirements to operate a collector. Will you have compressed air readily available where the collector is going to be installed? How often will the dust collector be run? Who will operate and maintain the dust collector? How much horsepower will the collector consume during operation? Can you minimize cost by only running the collector when dust is being generated? Is it possible to employ variable frequency drive technology with the collector, rather than a damper to further reduce operating costs? Will the collector being offered by the supplier meet any specific air quality for the outlet emissions? How will you monitor that air quality level?
4. What Should You Consider to Ensure the Smoothest Installation?
The primary factors for ease of installation are typically the size of the dust collector and the location the collector will be installed. Large, centralized collectors represent one end of the spectrum; requiring one or more cranes and an installing contractor to fabricate and install ducts and associated equipment. If you can accomplish your needs with smaller collectors or possibly plug-and-go units located either at or very close to the point of dust creation, you can limit or possibly eliminate the need for ductwork. This reduces installation to a fork truck and the necessary routing of electrical and compressed air supplies to the collector.
Understanding the process, localizing dust collection, and minimizing collector size all help simplify installation of collectors and their associated equipment. In addition, a review of the collector’s Installation and Operation Manual before installation starts can identify tools and/or unique items necessary for a smooth installation. This review can also highlight sequences of assembly that can simplify installation. As an example, collectors often have hopper and leg sets that need to be assembled on the job site. In some cases, assembling the sections is easier if the hopper starts out upside-down and the entire unit is inverted after the legs are attached. In other instances, it is easier to assemble the legs and then lower the hopper onto the leg pack. The Installation, Operation, and Maintenance manual will often illustrate these and other assembly details.
5. How Can You Get Good Value for Your Money?
Unfortunately, just installing a dust collector does not complete your dust collection strategy. You will be operating the collector for the life of your process. This means that beyond the dust collector’s capital cost, you should consider the operational costs to ensure you’re considering the best value over the full life cycle of your dust collection system.
Replacement filters or parts, lost production due to downtime, and energy consumption during operation are all costs and expenses that add up quickly. To find the best collector fit for your process, work with your dust collector supplier to compare initial and operational costs of different collectors.
The style of collector you select may influence the energy required to filter the air. Filters operating at lower stable pressure drop require less frequent cleaning, often last longer, and typically reduce the power required to pull air through your dust collection system. Sometimes several smaller collectors dedicated to portions of your operation will save operating expense without increasing capital cost. In other situations, centralized collectors may offer benefits in ease of service. Ensure you explore options in collector style, location, and design before you make any purchase.
Ask your collector supplier who will be able to help if technical issues arise.
6. What Kind of Support Should You Expect from Your Collector Supplier After the Sale and Installation?
In considering the operational costs of a collector, remember you will eventually need to order new filters or replacement parts. Obtaining a list of common replacement parts from your dust collector supplier will help you understand what items you may need to purchase in the future. Determine if these parts are kept in stock with your supplier, or if you will need to purchase and inventory them yourself. Ask if you need to work through an aftermarket sales representative to purchase items or if the items are available through other supply channels. You may also want to proactively learn from the collector supplier—who will be available to help if technical issues arise or assistance is needed—and how you would go about contacting them.
Selecting and installing a dust collector will be a decision you live with for many years. Taking the time to evaluate your needs and the alternatives available for dust collection will provide benefits for years to come. That investment lets you make a well-informed decision that could reduce your initial costs and increase your ongoing satisfaction with the dust collection system. And when it comes to purchasing a dust collector, it doesn’t get much better than that.
7. When Should You Consider IoT for Your Operation?
When the solution can help improve uptime. If you know the cost of your hourly downtime, it is easier to prioritize IoT projects that keep you up and running. In a survey sponsored by Donaldson, 38% of facility engineers reported that, if their dust collector fails, their production line must shut down—at an average cost of $3,700 per hour. If your facility requires a reliable dust collector, calculate your downtime costs and compare them with the costs of subscribing to an IoT-enabled monitoring service.
When it can help reduce cost of equipment ownership. Ask yourself if the IoT solution will pay off in longer-lasting equipment or parts. In dust collectors, for example, filters may last longer with proper monitoring. One facility we work with was having to replace filters every six weeks and could not identify the cause. With connected monitoring, the issue became clear: inadequate compressed air pressure. The facility was able to address the issue and restore filter life to approximately one year. Where could real-time information help reduce your recurring costs?
When it can assist with improving regulatory compliance. Are you tasked with reporting data about your dust collector performance to a local, state, or federal authority having jurisdiction? You may often have to spend time walking to dust collectors and manually recording data, then later manually entering that data for storage. This is a time-consuming process that can lead to outdated reports or human errors. A connected dust collector automates data collection on factors such as differential pressure. This ensures up-to-date information during an audit, and reduces the errors often associated with manual entry.
Summary
In short, ask where a connected solution can spare you downtime, reduce equipment costs, and/or help you comply with regulations. With any or all of these benefits, an IoT solution may be a sound investment.
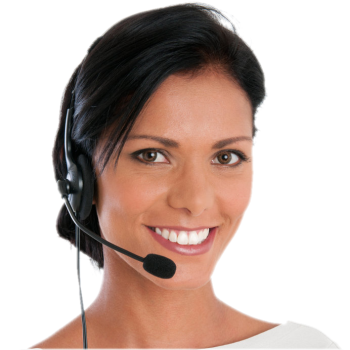
AST Canada has been helping clients find solutions for their unique Dust, Mist & Fume Collection needs for more than 40 years.
We can help you too.
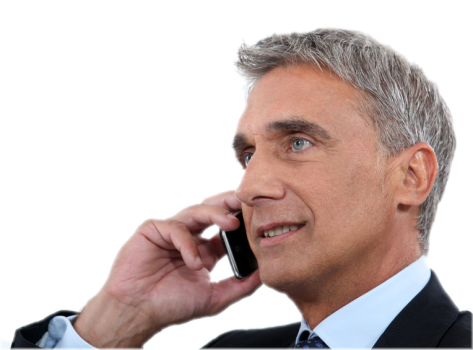